Highlights
- As a global manufacturer, we recognize our impacts extend beyond our operations. We believe it is our responsibility to engage suppliers that are committed to the highest sustainability standards and values.
- We achieved our FY2024 target of assessing sustainability performance of 60% of our supplier spend. By the end of the fiscal year, we assessed 61% of our supplier spend.
- We incorporate our Supplier Code of Conduct into all purchase orders to communicate our expectations to our suppliers.
- Greif joined the Sustainable Purchasing Leadership Council (SPLC) in 2024 to support our efforts in sourcing sustainable products.
Why Supply Chain Management Matters
Greif believes we have a responsibility to engage our suppliers around the globe as part of our commitment to sustainability. We communicate our expectations to our suppliers through our Supplier Code of Conduct, striving to uphold high levels of integrity, accountability, and dedication to sustainability throughout our supply chain. We aim to source high-quality, market-competitive materials while continuously looking for opportunities to better serve our customers.
Effective supply chain management enables us to realize efficiencies for our customers and streamline product delivery, supporting our delivery of quality, low-cost products. Our supply chain partners are critical to our ability to deliver circular and lower-carbon products. By working collaboratively with our suppliers and customers, we monitor and mitigate our environmental and social impacts while building resilience into our maturing supply chain.
Our Approach
Our Global Supply Chain (GSC) Sustainability program consists of three pillars outlining how the GSC team will achieve an ethical supply chain while advancing Greif’s sustainable growth.
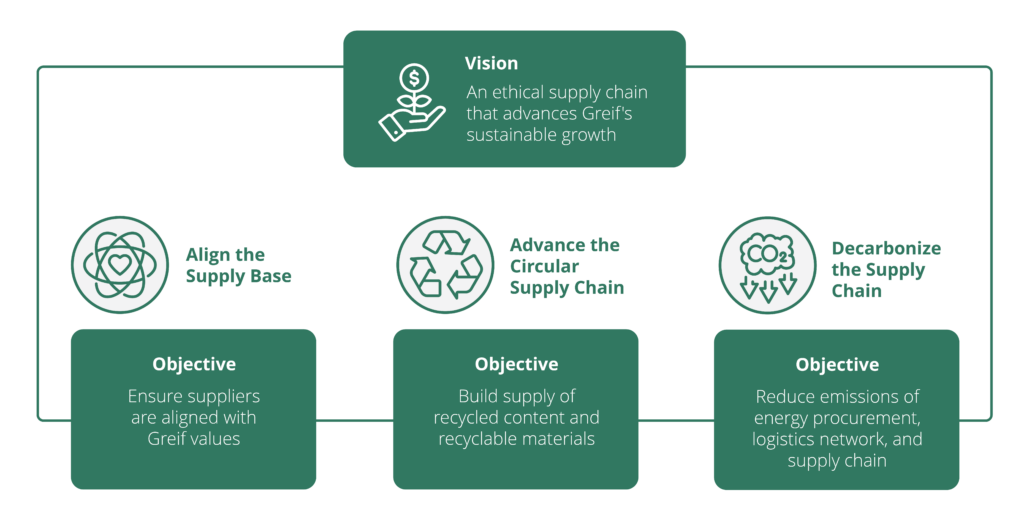
Greif’s colleagues, from logistics managers to sourcing managers, are critical to the success of the GSC Sustainability program. To keep our colleagues informed and trained on supply chain sustainability topics, we provide education to 100 percent of GSC colleagues, including the entire sourcing team. Through our internal upskilling platform Greif University, we offer self-paced training to any Greif colleague interested in learning more about carbon emissions reporting, supply chain sustainability regulations, and related topics.
Compliance with applicable laws to prevent potential human rights violations in our supply chain is foundational to our GSC management strategy. Each year, we validate our Conflict Minerals Policy with our legal and supply chain teams, and, in 2024, we published a revised Conflict Minerals Policy. We assess conflict risk across our supply chain with suppliers that use tin in their operations and publish our Conflict Minerals Report annually. For more information, visit our 2023 Conflict Minerals Report.
Measures outlined in our Supplier Code of Conduct and Transparency in Supply Chain Disclosure indicate Greif also abides by the California Transparency in Supply Chains Act of 2010, which prevents and eliminates forced labor in our direct supply chain. Our Ethics Hotline is available to anyone, internally or externally, who wishes to report concerns within our value chain.
GSC Sustainability Pillar Performance
Align the Supply Base
To increase our suppliers’ alignment with Greif’s values and expectations, we regularly communicate with our suppliers about our Supplier Code of Conduct. We make updates to the Code every 2-3 years, including scope expansions, language revisions, and the incorporation of new environmental or social risks faced by key industries. Greif communicates these updates to our business partners and provides an opportunity for suppliers to agree to the updates. Our next update will take place in 2025.
To validate that our suppliers are upholding our expectations, we expanded our due diligence procedures in 2024. We invested in a risk management platform, enriching our supplier data to identify risks within our value chain. This platform allows us to assess suppliers further to verify they are addressing risks, confirm they are meeting our minimum standards, and empower our sourcing managers to make data-driven decisions about their commodity’s value chain. Using our enriched due diligence process, we assessed 61 percent of our suppliers by spend for sustainability performance in 2024.
We recognize that, as we assess our suppliers, we are also being assessed by our customers. To be the supplier of choice, we are committed to decreasing risk across our value chain. Expanding our due diligence processes and improving the depth of our supplier risk data has allowed Greif to minimize geopolitical risks that could lead to supply chain disruptions and enabled us to continue delivering exceptional customer service. As regulations and industry risks evolve, we remain committed to bettering our due diligence processes for the benefit of our organization and all the customers we serve. Greif is committed to improving our supply chain management strategies and building a more resilient and sustainable supply chain.
Greif’s Inaugural Supplier Summit
In 2024, we led our first Supplier Summit Event, hosting over 220 leaders from 125 of our key strategic suppliers. The theme of the summit was “Be the Advantage”, driving home the goal of the event: to join together with our supply partners and ideate solutions to drive value for all organizations. The hosting Global Supply Chain team joined Greif’s Executive Leadership Team and colleagues from finance, operations, legal, commercial, human resources, and digital technology.
We began the inaugural summit by introducing Greif’s structure, values, and strategic priorities, emphasizing that success is a product of suppliers and Greif understanding each other’s businesses better. We conducted break-out workshops and reviewed the supply chain strategy roadmaps for the logistics, purchasing, sourcing, and responsible supply chain functions. Our team hosted one-on-one meetings in which we explored the targets, initiatives, and gaps in our supply chain management. Our conversations focused on mutual understanding and collaboration. Throughout the summit, we gained a better understanding of our suppliers’ capabilities and priorities, finding alignment and identifying opportunities for joint project development.
Through the summit, we also gained knowledge about environmental and social risks and opportunities across our supply chain. Following the Summit, we conducted formal engagement with key suppliers to address these risks and opportunities. We were excited to conclude the Supplier Summit by awarding the first Greif Supplier Awards to suppliers that delivered great value in our 2024 supply year. To learn more about the event, visit our press release.
- Excellence in Direct Materials: ArcelorMittal Europe Flat Products, MaxSteel, Borçelik, ExxonMobil, Nalco/EcoLab, Dow, Aalterpaint, Berger Global
- Excellence in Indirect Materials: Coupa, Reworld, Merco Machines, Multipli Machines, Advantage xPO, Motion Industries
- Excellence in Responsible Supply Chain: Solenis
- Excellence in Logistics: C.H. Robinson, Cowan Systems, LLC, Menzies Distributions Solutions, LTD, GLM Transport, Inc
Advance the Circular Supply Chain
Advancing circularity remains essential to our supply chain management strategy. In 2024, we worked with our subsidiary, Ipackchem, to accelerate our sourcing and management of post-consumer resin (PCR). Our efforts are guided by EU regulations, including the new Packaging and Packaging Waste Regulation (PPWR), which provides a framework for increasing PCR content in packaging materials. We currently use PCR in Greif products including IBCs, small and large plastics drums, jerrycans, and pallets. But, as we continue to improve and scale, we aim to increase the quantity of PCR in these plastics products. Not only will increased PCR reduce our consumption of virgin resin and reduce plastic pollution, but it also reduces the emissions in our products’ carbon footprint, delivering benefits to both Greif and our customers.
In addition to increasing the recycled content of our jerrycans, small and large drums, and IBCs, we also strive to increase the recycled content of our steel drums. In 2024, we partnered with key steel suppliers to trial steel made by electric arc furnace production. Electric arc furnace production generates steel made from higher recycled content, decreasing carbon emissions and increasing the ratio of recycled material. This initiative addresses both our circularity and decarbonization pillars. We plan to run more trials in 2025.
Decarbonize the Supply Chain
The GSC team is dedicated to identifying, evaluating, and executing projects that reduce carbon emissions in our supply chain. In pursuit of our commitments, we have the potential to reduce emissions in three key areas of our supply chain: energy procurement, logistics network, and raw material sourcing.
Through our energy procurement teams, we develop and execute emission reduction projects to drive down our Scope 2 emissions. These projects include Power Purchase Agreements (PPAs), Virtual Power Purchase Agreements (VPPAs), and other renewable energy options on the market. To learn more about our achievements in energy procurement, please see the Climate Strategy section of this report.
In addition to overall emissions reductions, one of our critical focus areas is our logistics footprint. This year, we engaged with customers and suppliers alike on identifying empty mile reduction. As a producer of packaging, some of our finished goods are collapsed and bundled for shipping to our customers, where they can open or assemble our products to be filled with their finished goods. However, many of the products we make are rigid packaging solutions, which we currently ship to our customers empty and ready to be filled. By partnering with our customers to understand their supply and delivery networks, we aim to find opportunities to reroute our own network to reduce our number of empty miles and when possible, return used customer packaging to our own reconditioning operations.
Knock Down Drums
Greif’s Knock Down Drums (KDDs) are designed to meet customer specifications while optimizing working capital, space utilization, and sustainability. We deliver these drums unassembled or semi-assembled, allowing for on-site assembly by our customers. This design allows for more efficient shipping and storage, as the drums take up less space and allow handling in a flat or partially disassembled form, reducing the consumers’ carbon footprint. For instance, a 40 F Container can fit up to 1720 KDDs but only 80 large steel drums. From a transportation perspective, this results in 88 percent savings in CO2e emissions. With several features available, the drums can be tailored to customer needs. Greif’s Knock Down Drums offer an affordable alternative to fully assembled drums, delivering savings in manufacturing and transportation.
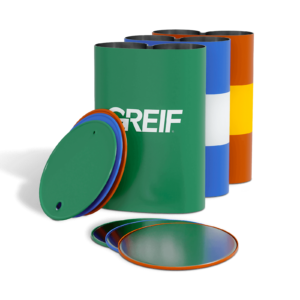
Given the large scope of our supply chain, we want to tap all opportunities for carbon emissions reduction. In 2024, we conducted a detailed Scope 3 emissions analysis to identify significant levers of impact to reduce emissions. Following this assessment, we are developing a pipeline of projects and investments to reduce Scope 3 emissions. To learn more about our Scope 3 analysis, please visit the Climate Strategy section.
Goals, Progress, & Performance
2030 Goal:
- Evaluate the sustainability performance for 80 percent of our total spend with suppliers.
In 2024, we assessed 61 percent of our suppliers by spend for sustainability performance, exceeding our annual target and making progress toward our 2030 goal. We recognize that volatility, uncertainty, complexity, and ambiguity can increase costs in a supply chain. To address these challenges, we evaluate climate, sustainability, financial, and geopolitical risks through our due diligence procedures.
We work to understand how suppliers are preparing and transitioning their manufacturing processes, facilities, and business continuity plans to effectively mitigate relevant risks. By enhancing visibility into our supply chain, we strengthen our relationships with suppliers and our risk mitigation plans. We also use this engagement to support suppliers in developing their own risk mitigation strategies.
Reducing supply chain risks is critical to controlling costs, allowing us to continue our legacy of legendary customer service.